Update
- Unfortunately, due to the coronavirus pandemic, we were unable to run the course on the proposed dates, so it's been postponed indefinitely.
Please click the image below to download the flyer with more details.
A blog with information and student feedback from the previous courses can be seen here:2017 course, 2014 course, 2013 course, 2011 course.
The course is supported by AFMWorkshop, The Faculty of Sciences of The University of Porto and my research institution, LAQV/Requimte.
- Details
- Hits: 20161
The last few years have seen quite a few changes in the AFM industry with some companies disappearing, and some others being acquired. presumably some caused by the financial crisis, which has certainly affected instrument spending.
Nanotec, a small Spanish company ceased trading in 2015. Nanotec were well-known for also producing their analysis software WSxM, which in addition to running their instruments, also opened almost all AFM image formats, and had a lot of great analysis features. Fortunately, WSxM is still available.
Keysight was a spin off of Agilent, and hosted the AFM division for a few years. unfortunately, they no longer make AFMs. Agilent had bought the IP of Molecular Imaging, which was one of the "big three" at one point. Agilent did continue to develop MI instruments for a number of years. Agilent had also bought the IP of Pacific Nanotechnology, but never did anything with it.
The biggest recent change is probably that Bruker bought JPK. JPK were early leaders in successful biological AFMs, and sold particularly well in Europe. As of now, Bruker are offering some of JPK's products and www.jpk.com still exists. I kind of hope this continues as their Nanowizard AFMs are good products. Bruker also bought Anasys instruments, which make Nano-infrared microscopes, and are now offered under the Bruker brand.
Asylum Research was acquired by Oxford Instruments, and are still trading under the name Asylum Research - An Oxford Instruments company.
Of course, in addition, a few smaller companies came and went as usual! All these changes are reflected in the page "Where to Buy - AFM Instruments", linked below.
I also link below to an interesting Post on LinkedIn from Paul West on the history of the AFM business, for those who are interested!
- Details
- Hits: 9658
In my job as a researcher using AFM, I often act as a scientific reviewer for papers describing AFM experiments. I also collaborate with many groups and spend a lot of time revising and correcting articles which contain AFM data. In this two part article, I’ll describe how you should go about preparing a scientific paper which contains AFM data.
NOTE: Some of this content is not really specific to AFM articles, but could be applied to any experimental scientific report. These parts should already be known to you if you are writing an scientific article, but many researchers are never taught how to correctly prepare a scientific article before they start writing them. For more general guides on preparing scientific articles, check here.
What are the overall requirements for an AFM paper?
-
Experimental conditions should be well described
-
Data should be presented in a useful format
-
Reproducibility should be addressed
-
Conclusions should be justified
These requirements may seem like “common sense”, but you might be surprised by the number of articles which are published but do not meet some, or even all of these criteria!
-
Experimental conditions:
What should this include:
Imaging mode used. This is rather important, since the results can be different from mode to mode. It also helps to make your data reproducible. Note that not all instruments use the same terms to refer to specific modes :This is particularly the case for tapping mode. It can be useful to use both the manufacturer’s name, and the most commonly used name for example: Imaging was carried out in AC-AFM (Tapping) mode.”
Instrument used. You should name the instrument mode and the manufacturer. You can also include the version of the instrument model, if applicable. Some journals still request the location of the company, but this is becoming optional e.g., you might write “Bruker Multimode 8 (Bruker, Newhaven, CA)”.
Probe used. The type of probe used can determine the type of information available, as well as the interaction force. Since there are many probes available on the market, it’s also useful to say the (approximate) frequency of the probe, which gives some idea of the type of probe, without he use looking up the details. E.g. you might say “AppNano ACT probes with around 300 kHz frequency were used”.
Software used. All AFM images require image processing, or analysis before presentation. It is a good idea to describe the software used for processing of the AFM data. You might also describe the processes used for analysis and /or data processing. E.g. you might say “Gwyddion 2.49 software was used for processing the images, and Roughness was calculated with the Gwyddion 'Statistical Parameters' tool".
Amount of data collected, and statistical significance. This issue is addressed below. However, it's worth remembering, that the microscopy images you collect should be representative of the sample(s). A part of the “materials and methods” section should be explaining this. For example, you might write “At least six areas per sample were imaged, and representative images are shown here.” If you have a variety of different images, you could add additional images to a “supporting information” section.
-
Presenting data in a useful format
There are many different types of AFM images, and different ways to display them. Very often the instrument will produce several different image channels, such as height, phase, etc. The most commonly used channel is probably height, since this is the only one with three-dimensional data. However, sometimes, it’s hard to make out the sample details in height images. For this reason, other channels, such as deflection or phase are often used. I recommend that the height image, always come accompanied with a z scale (normally it’s a colour gradient), and they should have either an inset scale bar, distance markers on the outside, or the legend must state the scan size (x and y). Examples are shown below.
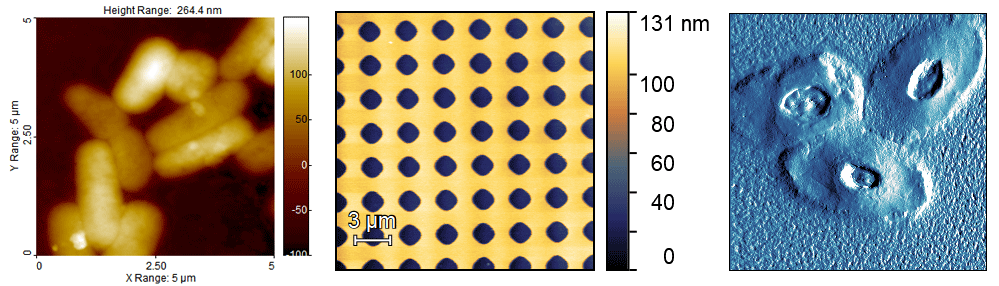
Does the colour I pick make any difference? No. You can choose which colours you like. For some reason, AFM images are “traditionally” shown in some shade of brown, but any colour scale is fine.
Should Amplitude/Deflection/Phase images have a z scale? No. The z scale on these channels is usually meaningless, as it might be in volts, or degrees, and in most conditions, is not needed. I recommend to remove it to avoid confusion.
Are the details you want to highlight easily visible? If not, the use of arrows to denote specific features in the image is recommended. The arrows should be referenced in the figure legend.
Talking of which, in part 2 of this article, I’ll talk about how a figure legend should be written, and how you should address reproducibility of the data, and draw appropriate conclusions from your results.
All images copyright peter Eaton 2019. Images produced with SPIP and Gwyddion software
- Details
- Hits: 10085
This is the second part of this article about how to write an academic paper including AFM data. If you have not already, you should read the first part here.
NOTE: Some of this content is not really specific to AFM articles, but could be applied to any experimental scientific report. These parts should already be known to you if you are writing an scientific article, but many researchers are never taught how to correctly prepare a scientific article before they start writing them. For more general guides on preparing scientific articles, check here.
Figure legend. The figure legend is an important part of the figure. It should not be too brief, e.g. “Figure 1. AFM images of samples 1 and 2.”. But it should also not be too long. It should be concise, but has to have all the information needed to enable the reader to understand the figure. It should have a description of the type of data, if necessary explain the scale of the images, and clearly identify the samples shown. For example, a good figure legend might be: “Figure 1. Representative tapping mode AFM images of samples 1 and 2. A: Height image of sample 1; B: Phase image of sample 1; C: Height image of sample 2; D: Phase image of sample 2. All images show 1????m x 1????m areas, and the z scales are indicated next to the height images. The arrows show the location of anomalous nanoparticles discussed in the text.”
-
Reproducibility
All numeric values included in the results must be accompanied by standard errors, or standard deviation of the means. You must also say how many measurements were made. It is important to discuss how many areas were imaged, and how often the features discussed in the text occurred. It’s not acceptable to show only one image, with the assumption that it represents a whole sample!
-
Conclusions
It should go without saying that the conlcusions you make based on your AFM data must be justified. This often means that you should calculate the occurrence of specific features, so if you want to say that the surface got rougher, or features grew after treatment, you should measure this, and show means, and errors, or a histogram of results. Note that histograms can help a lot with non standard data distributions, i.e. where there are outliers.
Can lateral measurements be used in AFM? Yes - but with caution, and only sometimes. If you have samples that are small, comparable to an AFM probe tip, lateral measurements of them will be wildly erroneous with AFM. For this reason it’s nearly always preferable to use vertical measurements where possible. Lateral measurements typically only work well for features much larger than the AFM probe, so you must be careful with these. One way to reduce the effect of these errors is to deconvolve the probe shape from your images. See section 2.3.4 of Atomic Force Microscopy.
If your conclusions are based on certain small features in your images, you can present your images in a way so as to make these features clear. This can be done by:
-
Cropping. A nice way to highlight certain features is to show a large image as well as a cropped section magnifying the feature you wish to show.
-
Histogram control. Control the height range shown in your height images to highlight the part you are interested in showing. So for example, if you wish to show tiny 20 nm features, you cannot do it with a z-scale of microns in a height image.
-
Shading. Light shading is a routine available in all AFM processing packages (such as SPIP and Gwyddion), which can highlight small topographic differences
-
Including error signals or phase images. These channels are frequently better for showing small details.
-
Highlighting with arrows. As discussed above.
-
Using unusual colour schemes. In general complex colour schemes make for confusing images, but for some images they can be appropriate, and help to illustrate the different features at different heights.
Some examples of these schemes are shown below.
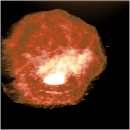
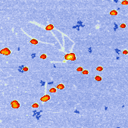
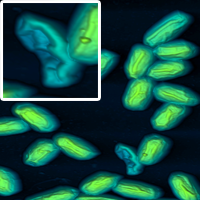
Good luck with your AFM articles! If you have more questions, contact me here.
NB. All the images in these two articles were produced with SPIP 6.7.7 or Gwyddion 2.40
This article and all content is copyright Peter Eaton and AFMHelp.com 2019.
- Details
- Hits: 15356
During our recent Porto AFM Training Workshop, we held a little competition, asking the students to produce and process the best images they could.
This year, the winner of the competition was Magdalena Scheibe, who produced this beautiful image of human hair. Well done, Magdalena!
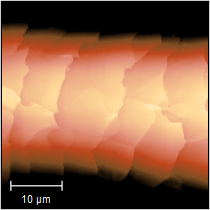
However, we must also acknowledge two very inventive submissions, firstly this Game of Thrones-inspired one from Izabela (scanned with Anita), which actually shows a "wall" of nanoparticles, and nicely processed in SPIP.
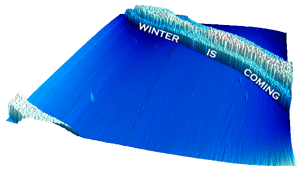
And finally, this "Moonlanding" on another hair surface from Sandra and Rita. Very nice!
Exploring Hair at the Nanoscale with AFM
Thanks to everyone who entered the competition!
All images Copyright AFMHelp.com and their respective creators.
- Details
- Hits: 5353
Subcategories
Page 4 of 21